Everything You Need to Know about Hypertherm Plasma Cutters
One of the most common ways to cut through various types of metal is with oxy-fuel cutting. There are also other ways of cutting through metal but they are less efficient and slower. But oxy-fuel cutting can easily be an alternative rather than the go-to option. If you choose to get a plasma cutter you will rely on a quick and easy method of cutting through metal workpieces.
A plasma cutter unlike any other cutter works thanks to heat compressed air. Like other cutters, a CNC Hypertherm plasma cutter relies on DC voltage for its operation. Plasma cutters work by ionising atoms at a very high temperature and thus it creates what is known as a plasma arc. This jet of plasma is what goes through the metal by melting it and pushing the molten metal away.
How to Choose the Right Hypertherm Plasma Cutter
Cut Rating
Not all plasma cutters use the same Hypertherm torch parts though which is why they don't all perform the same. This is why you need to consider certain factors such as cut rating. The cut rating is one of the most important features of a quality Hypertherm plasma cutter. There are three types of cut ratings a plasma cutter can have. These are rated cut, quality cut, and sever cut.
A plasma cutter with a rated cut refers to the thickness of a metal that can be cut at a rate of 254 millimetres per minute. A cutter with a quality cit rating refers to the thickness of a metal that is going to be cut at a speed lower than 254 millimetres per minute. A Quality cut rated cutter is able to cut through thicker workpieces. Sever cut rated plasma cutters are able to cut the thickest metal pieces but their cutting speed is a lot slower and the cut itself may not always be clean.
Voltage
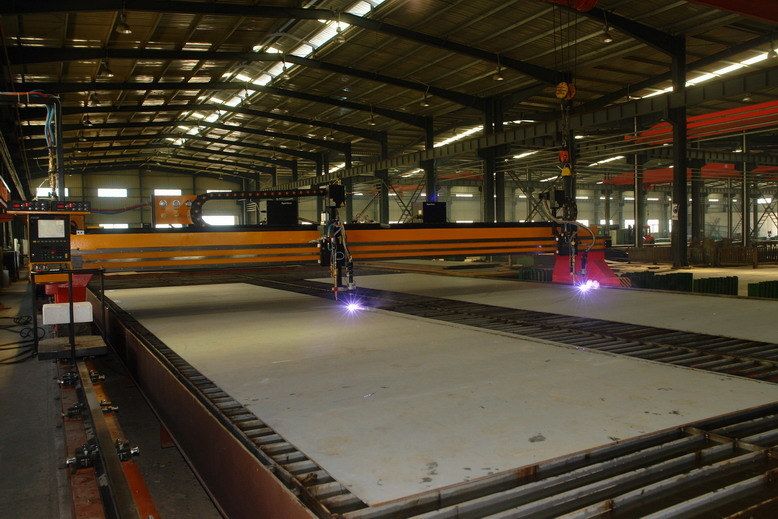
A CNC Hypertherm plasma cutter can come with three different voltage options. These are 115V, 230V and a dual voltage option. If you go for a 115V cutter you will be able to cut with less power which makes it a good choice for beginners. 230V cutters are more powerful and you need a generator to run them which is why pros is them more. But if you want more versatility go with the third option, a dual voltage cutter that lets you work with both the 115V and 230V of input.
Duty Cycle
The duty cycle of a plasma cutter provides you with the amount of time the cutter can work for in one go. If your plasma cutter has a higher duty cycle it means it can be used for longer periods of time without experiencing a drop in voltage.
Air Compressor
Since plasma cutters require compressed air in order to function you need to consider having an air compressor. An air compressor can be included with a CNC Hypertherm plasma cutter or you may need to get one separately. Built-in air compressors are going to increase the cost of the cutter but you will be able to use the take small jobs and do them quickly.
Weight
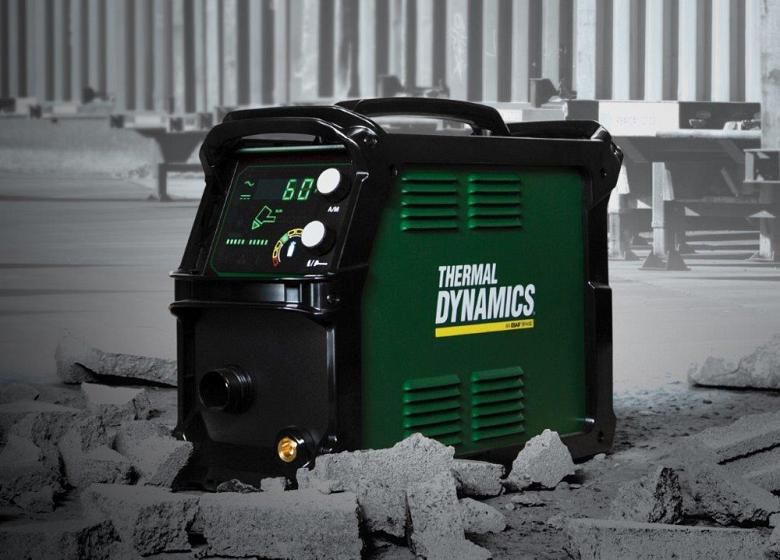
The weight of a Hypertherm plasma cutter is going to determine its use. If you get a 45 kg heavy cutter you'll be able to use it for industrial applications. Usually, plasma cutters start at around 9 or 10 kg, which are some of the lightest you can get. Keep in mind that these plasma cutters are not that powerful.
Cut Quality
The cut quality of a plasma arc cutter is going to depend on how clean and smooth the finished cut is. Some of the best plasma cutters are going to have a high cut quality, meaning the cuts you make with them are going to be so clean and sharp that you won't need to clean or smoothen them out.
Pilot Arc
If your plasma cutter comes with a pilot arc feature then you will have a more stable arc with a longer consumable life. This is because this cutting feature allows you to cut metal without the tip of the torch ever striking the metal piece. This can be beneficial when cutting metals with rusty surfaces, in this case, you won't have to clean the rust from the metal beforehand.
Using a Hypertherm Plasma Cutter
Preparation
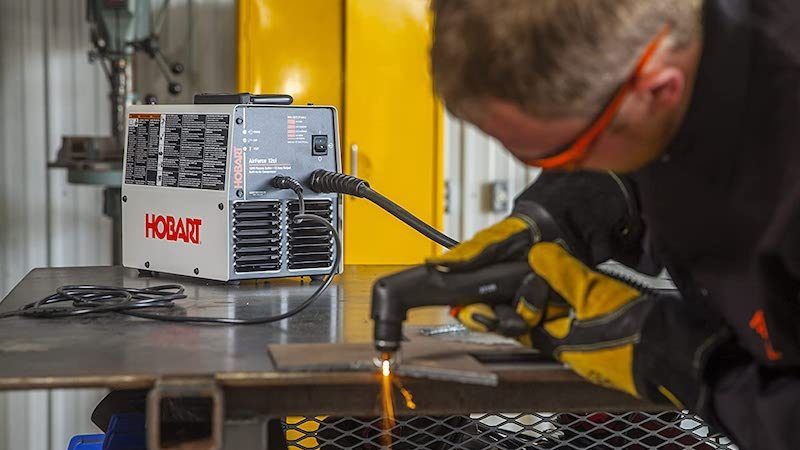
Always ensure that before you use a plasma cutter you inspect the torch ti, shield cup and electrode. You should also check the gas/ air pressure at the compressor and grind off any paint or rust found on the surface of the metal you'll be working on.
Cutting
1. To cut using a plasma cutter you should place the drag shield on the edge of the metal and direct the arc straight down. Once you do that, raise the trigger lock and press the trigger. When the arc starts, start by slowly moving the torch across the metal.
2. Make sure to adjust your speed as you go so the sparks being generated go through the base metal and out of the bottom of the cut. When you are at the end of the cut, make sure to angle the torch slightly towards the edge. You can also pause for a brief moment before you release the trigger.
3. At the end of the cut, let the torch cool down for about 20 to 30 seconds. This will let the post-flow air go away and you can start using the cutter again. Doing so otherwise will restart the arc and this is not what you want to do.